Mold Injection Plastic: Transforming Manufacturing Efficiency
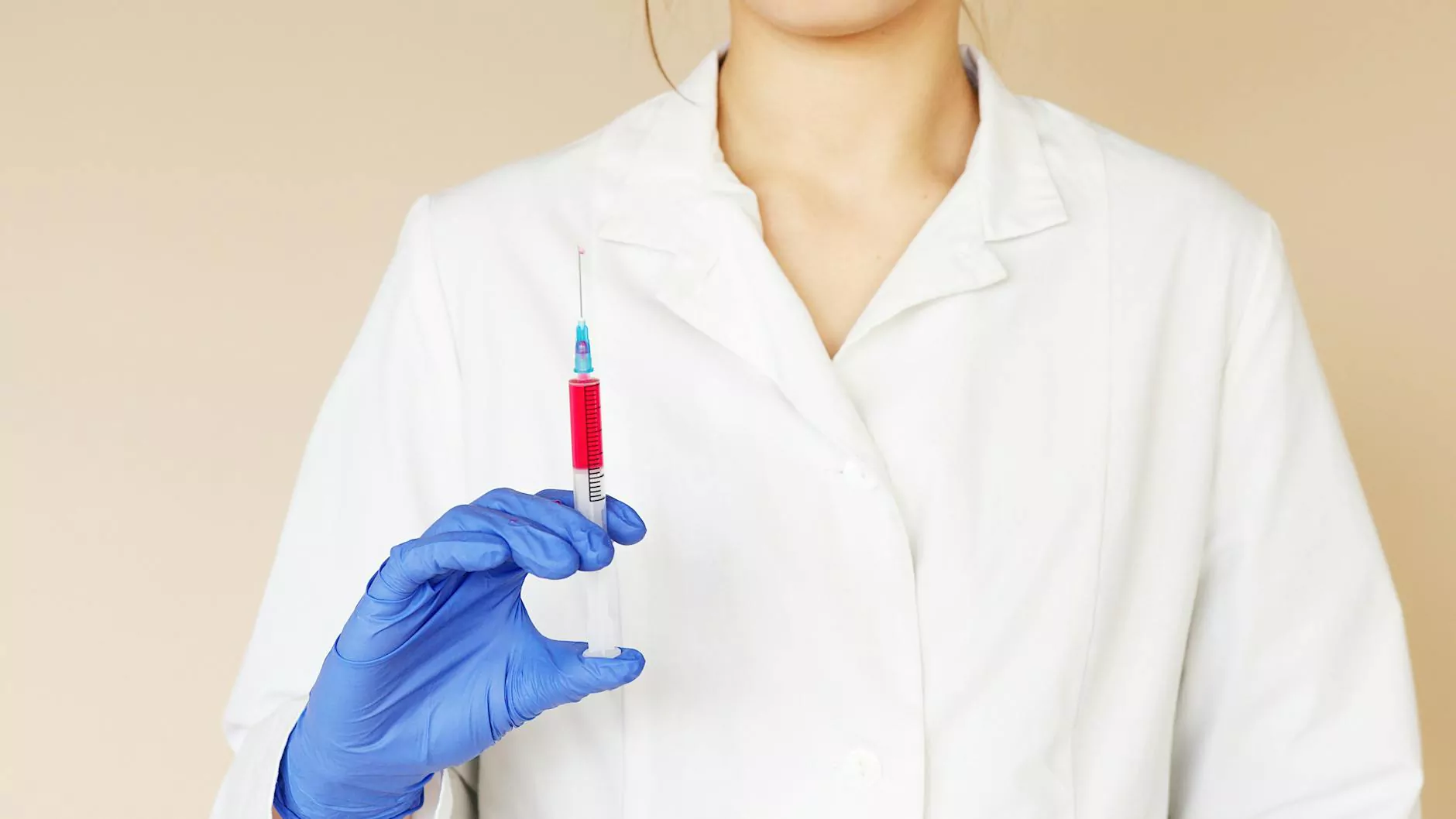
Understanding Mold Injection Plastic
Mold injection plastic is a revolutionary manufacturing process that utilizes high pressure to inject molten plastic material into a mold. This method allows for the creation of complex shapes and components that are essential in modern manufacturing. The process has significantly evolved over the years, becoming a cornerstone in industries ranging from automotive to consumer goods.
The Process of Mold Injection
Steps Involved in Mold Injection Plastic
- Designing the Mold: The first step is to create a detailed design of the mold using CAD software. This design must consider the specifications, material properties, and anticipated production volume.
- Material Selection: The type of plastic used is crucial. Engineers must select a plastic material that suits the functionality and durability required for the end product.
- Mold Fabrication: Once the design is approved, the mold is fabricated. This can be done using various techniques, including CNC machining or 3D printing.
- Injection Process: The plastic pellets are heated until they become molten, and then injected into the mold under high pressure.
- Cooling and Solidification: The injected plastic is allowed to cool and solidify within the mold, taking its final shape.
- Demolding: Once cooled, the mold is opened, allowing the finished part to be removed.
- Post-Processing: Any necessary finishing steps, such as trimming, assembly, or painting, are performed on the molded parts.
Benefits of Mold Injection Plastic
Efficiency and Precision
One of the key advantages of mold injection plastic is its ability to produce high volumes of parts with remarkable precision. The process minimizes waste, as the material is used efficiently. Furthermore, the speed of production allows manufacturers to meet consumer demands swiftly.
Cost-Effectiveness
While the initial costs for mold creation can be high, the per-unit cost significantly drops with large production runs. This economy of scale makes mold injection plastic an attractive option for manufacturers looking to optimize their budgets without sacrificing quality.
Design Flexibility
Another significant benefit is the design flexibility that mold injection plastic offers. Complex geometries can be easily achieved, allowing designers the freedom to innovate and create customized products efficiently.
Applications of Mold Injection Plastic in Metal Fabrication
The impact of mold injection plastic extends beyond traditional plastic products. In metal fabrication, mold injection is increasingly used to create intricate components that complement metal parts.
Example Applications
- Automotive Industry: Mold injected plastic components are used for dashboards, panels, and other intricate parts, enhancing both performance and aesthetics.
- Consumer Electronics: From phone casings to intricate internal components, the precision of mold injection plastic is invaluable in the production of electronics.
- Medical Devices: In the medical field, custom plastic components are crucial for equipment accuracy and safety, and mold injection provides the precision required.
Mold Injection Plastic vs. Other Manufacturing Methods
While there are numerous manufacturing methods available, such as blow molding and extrusion, mold injection plastic is often preferred for its combination of speed, accuracy, and versatility. Here's a comparison:
Key Comparisons
CharacteristicMold Injection PlasticBlow MoldingExtrusionProduction SpeedHighModerateHighMaterial WasteMinimalHigherModerateDesign FlexibilityHighModerateLowEnvironmental Considerations in Mold Injection Plastic
As with any manufacturing process, environmental impact is a significant concern. Fortunately, advancements in technology have made it easier to minimize the ecological footprint of mold injection plastic. Manufacturers can implement:
- Recyclable Materials: Many plastics used in mold injection can be recycled, reducing waste and promoting sustainability.
- Energy Efficient Processes: Optimizing the machinery and process parameters can lead to significant energy savings.
- Eco-Friendly Additives: Using biodegradable materials and eco-friendly additives is a growing trend to lessen the environmental impact.
The Future of Mold Injection Plastic
The future of mold injection plastic looks bright, with continuous innovations shaping the landscape of manufacturing. With the rise of technologies such as 3D printing and automation, we can expect even greater efficiencies, reduced lead times, and innovative designs that were previously unimaginable.
Innovation in Materials
The development of new materials, including bio-based and recycled plastics, is at the forefront. These materials not only meet the demands of performance but also contribute to environmental sustainability.
Automation and Intelligent Manufacturing
Integrating automation in the mold injection process allows for real-time monitoring and adjustments, ensuring precision and accuracy while drastically reducing production time.
Conclusion
In conclusion, mold injection plastic is a pivotal technology in the realm of manufacturing and metal fabrication. Its advantages—ranging from efficiency to cost-effectiveness—make it an essential process for industries seeking to innovate and meet the evolving demands of the marketplace. As the industry progresses, embracing sustainability and technological advancements will be key, ensuring that mold injection plastic remains at the forefront of manufacturing excellence.
For more information about how mold injection plastic can enhance your manufacturing processes, visit Deep Mould.